Electrocycling GmbH obtains valuable raw materials from electronic waste
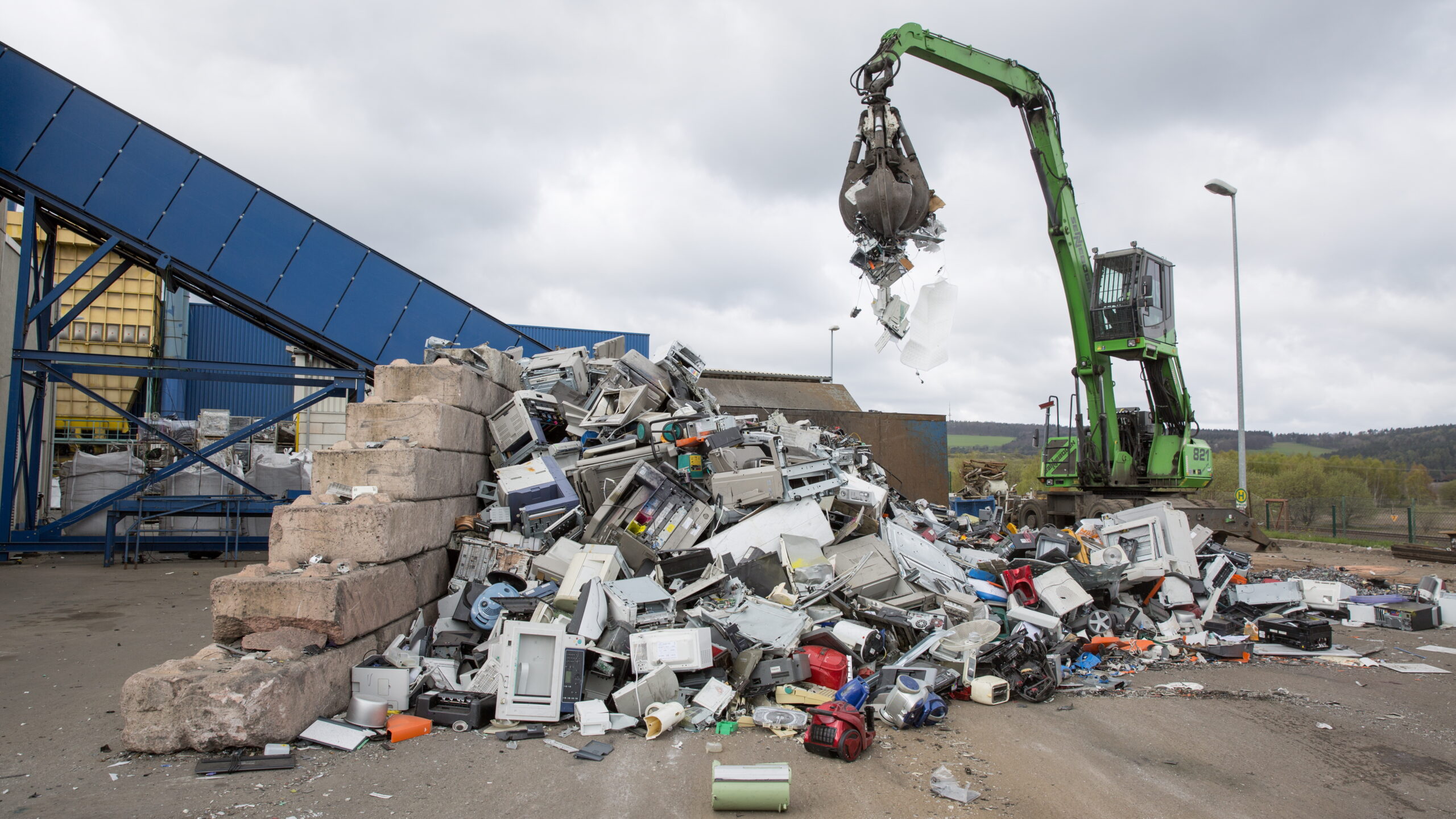
12.03.2024
Hunting for treasure
Hi-fi systems, computers, telephones: the symbols of our electronic age are piled high on the site of Electrocycling GmbH in Goslar. The company’s operations represent a treasure hunt, because all this scrap contains valuable raw materials. These are extracted in a sophisticated process and processed for re-use. HANSA‑FLEX also plays a part in making sure that the recycling operations run smoothly, because the heavy machinery which keeps them going – from the wheel loaders to the shredder – run on complex hydraulics.
The noise is deafening when, suspended from the arm of an excavator, a mechanical grabber digs into a pile of electronic waste. It then allows the various appliances to crash down onto a conveyor belt. The joints in the arm and the teeth of the grabber are moved hydraulically. “The pressure in the hose lines of this heavy-duty machinery can reach up to 400 bar“, reports Thomas Henze, works manager at Electrocycling. “This is where quality is essential.” It’s therefore no surprise that the company has been relying on HANSA‑FLEX as its hydraulics partner for over 12 years now.
Recovery of valuable raw materials
The first step is to separate the electronic waste into materials which contain harmful substances and those which don’t. The lead from the tubes of old televisions has to be disposed of separately, as has the mercury in relays or PCBs from condensers. Before the actual recycling process, oil or batteries also have to be removed so that they can’t contaminate the environment. It was in fact environmental protection which was the driving idea behind the establishment of Electrocycling GmbH. In the early Nineties Deutsche Telekom was looking for a way of recycling old telephones and connecting equipment. It then founded the company as a joint venture with other partners, including Preussag AG with its mining experience. On the basis of Preussag’s expertise in mining technology an efficient method was developed for the recovery of valuable raw materials from electronic scrap. With a workforce of 180, Electrocycling processes over 4,000 tonnes of electronic waste every month.
A massive strain on the hydraulics
Once the waste has been sorted an excavator picks it up with a huge shovel and transports it to the shredder. Like the other transport vehicles, it operates under rough industrial conditions, with the hose lines of the hydraulic system subject to an especially heavy load. “Any mechanical breakdowns interrupt operations and have to be repaired as quickly as possible”, explains Henze. This is why he appreciates speed and reliability in his hydraulics partner. “A phone call is all it takes and we can pick up the replacement hoses immediately.” The X-CODE system is especially useful in this respect. “We have recorded all hose lines with the alphanumerical X-CODE, making them immediately identifiable”, reports Otto Greibig from the HANSA‑FLEX branch in Goslar. This effectively avoids any mixups when orders are placed.
Hydraulic cylinders in the shredder
In the shredder a hydraulically controlled roller draws in the electronic waste. The material is then beaten by steel hammers, reducing it in the first phase to pieces sized between 50 and 100 mm. “Iron and aluminium are released relatively quickly,” comments Henze. The iron is separated from the other materials by magnets, and aluminium by eddy current separation. Because the magnetism of stainless steel components is relatively low, high-intensity magnets are used to separate them out. As they are in constant operation the steel hammers of the shredder are subject to wear and tear and have to be replaced regularly. In order to reach the interior of the installation, the upper section of the drum of the shredder is raised by two powerful hydraulic cylinders. “There’s a lot of power in operation there,” states Henze.
Returned to the economic cycle
After the iron, steel and aluminium have been separated out, the waste is reduced in a further stage to granules sized 10 to 20 mm. Now the non-ferrous metals such as copper and brass are separated from the remaining scrap, and can be extracted by measuring the density of the material. The non-ferrous granulate also contains precious metals such as gold, silver and palladium. These are sent by Electrocycling to a copper foundry, where the metals are sorted. In this way the company returns to economic use all metals and even homogeneous plastics, which are also separated out by a density separation process. Thermal utilisation is only applied in the case of some composite plastics.
Extremely worthwhile
Over the past 23 years Electrocycling has continued to refine its processes. This makes a great deal of sense, because many of the raw materials contained in electronic waste are as valuable as they are rare. “In the Nineties these old appliances had a higher precious metal content”, reports Henze, “but even today they still contain plenty of valuable materials”. On average current electronic waste has an iron content of around 30%. The aluminium content amounts to 8 – 9%, while the amount of non-ferrous metal granulate lies between 6 and 7%. A comparison with the mining industry shows how useful recycling in this field is: in order to obtain a tonne of copper, around 1,000 tonnes of rock has to be moved in opencast mining. Electrocycling can obtain the same volume of copper from 20 tonnes of electronic waste.
Learn more
- 12.03.2024
A real challenge
HANSA-FLEX is a Zeppelin service partner for Cat construction machinery and enginesFind out more - 12.03.2024
Softly whisper the leaves
BSR is the largest municipal waste disposal company in Germany and one of the 15 largest employers in the German capital.Find out more